Sustainability Report: Are Composite Building Materials Sustainable?
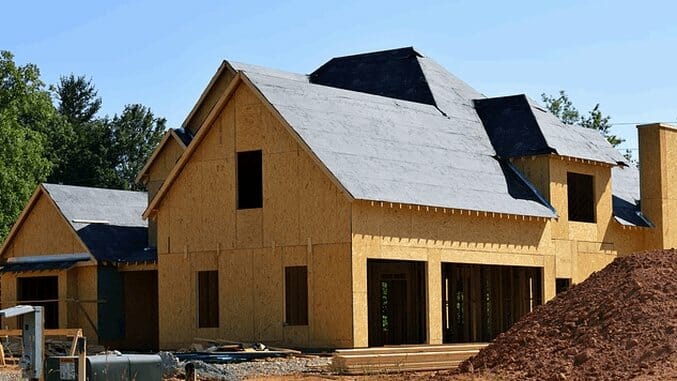
In grade schools long ago, many people had to build something out of toothpicks or Popsicle sticks—a house, a bridge, a boat. It might have been an art project or a science experiment, but the idea was to make something new out of existing materials. That’s the basic idea behind composite building materials, engineering a combination of materials that result in something better than the constituent parts.
“The components of cement concrete are aggregates (crushed stone, gravel, sand), cement, water, coloring and chemical additives (to control setting time and workability)…. On a per unit basis, cement is the most energy- and pollution-intensive component of concrete.” Arpad Horvath, Department of Civil and Environmental Engineering, University of California. (Photo courtesy of Anna Waldl / Pixabay CC0)
Concrete is a traditional composite created by combining aggregate, cement, additives and water. But as concerns grow about pollution, groundwater contamination and depletion of natural resources, the construction industry is rethinking its approach to building as usual. Composite building materials provide one alternative touted as a “green building” option.
Some newer composites are going mainstream—wood-like boards made of recycled plastic, or a combination of wood and plastic are commonly used for building outdoor decks. But the construction industry is slow to change, according to Arpad Horvath, professor in the Engineering and Management program at the University of California. In “Construction Materials and the Environment” he says construction companies, with the exception of some larger firms, are “ill-prepared” to address environmental management and stewardship.
“By virtue of its size, construction is one of the largest users of energy, material resources, and water, and it is a formidable polluter,” Horvath says. “Just how large is still being debated because information and data about the environmental impacts of the built environment are still not being collected and analyzed systematically.”
Safety First
Numerous composites have been developed and used successfully for years in other countries, such as cross-laminated timber. CLT is made of numerous pieces of wood, such as 2X4s or 2X6s, stacked crosswise and glued to create a larger, stronger piece of wood. Developed in Europe over 20 years ago, CLT is used there for all kinds of building projects. It’s proven to be cost-effective and has the added benefits of quick installation, reduced waste, improved thermal performance and design versatility. But most U.S. building codes won’t allow the use of CLT until more research and testing prove it meets our safety and building-code standards.
One of those requirements is how composite materials behave during earthquakes. At the University of Alabama, the Department of Civil, Construction and Environmental Engineering is doing seismic testing on CLT with the goal of “optimizing how much CLT and how much light-frame in the building that will make it work best,” says Thang Dao, assistant professor of structural engineering.
The familiar wall construction of vertical, 2-inch by 4-inch (2X4) wood studs spaced eight to 12 inches apart is called light-frame construction. It can’t hold up much weight, so it isn’t used in large buildings or high-rise construction. However, it does help a building withstand earthquakes fairly well.
“About 90 percent of U.S. residential structures are light wood-frame structures,” he says. “When you build higher, you need a structure that can carry a heavier load. In Europe they did some shake-table tests, and it performed very well (according) to European standards. When we brought it to the U.S., we modified it to meet the U.S. design codes and wood product specifications.”